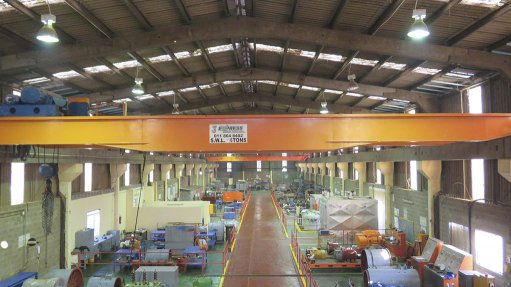
A new 435 m² machine shop workshop and transformer department at Marthinusen & Coutts’ facility in Kitwe, Zambia will further improve the quality and turnaround time of its offerings in the region.
According to Marthinusen & Coutts Zambia general manager Eugene Lottering, the commissioning of the machine shop workshop in January this year created significant space in the 1700 m² main workshop, allowing for the investment in a transformer department.
“We now have a dedicated factory for machining work-pieces for the main shop,” says Lottering. “The Marthinusen & Coutts head office in Johannesburg makes a vital contribution by sending their machine shop foreman to provide training. This upgrades the local Zambian machining skills on a continual basis.”
The division’s machine shop facility boasts five machining lathes, two milling machines, and a submerged arc welding machine. It also has a 50 tonne horizontal press and rotor binding machine. All equipment operates under two 6,3 tonne jib cranes.
“Our transformer department has allowed us to enter the market in transformer repairs. The facility is equipped with a 20 tonne overhead crane to lift larger transformers,” he says.
The new department is equipped with a new coil machine, ratio tester, an oil purification machine and a dedicated oven.
Marthinusen & Coutts, a division of ACTOM (Pty) Ltd has already successfully overhauled transformers for a number of opencast mines. This included a 10 MVA unit, two 5 MVA units and a 3 MVA unit. Working in collaboration with M&C Johannesburg has ensured quality is maintained, while local transformer repair skills are also being developed.
“We have also established a Level 3 maintenance site services team to provide on-site electro-mechanical assistance to customers,” says Lottering. “This includes on-site repairs, maintenance and testing.”
Significant previous investments in the division’s Kitwe workshop have included a 12 tonne balancing machine, a vacuum pressure impregnation (VPI) plant, burn-off and curing ovens, and a fan test column. There is also an AC and DC test facility, equipped with power analyser, surge comparison tester, core flux tester and high voltage pressure tester.
“Our continuous investment in the region allows us to provide customers with a one-stop electro-mechanical repair facility for alternators, generators, motors and transformers, as well as mechanical equipment,” he says. “This means shorter lead times and less transportation risk, while also benefitting the Zambian economy.”