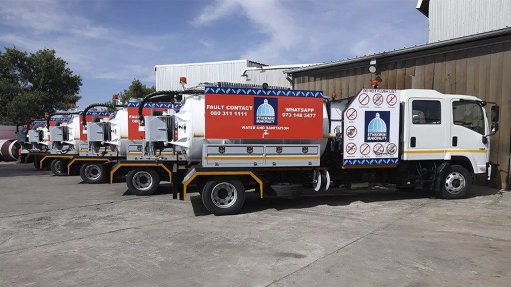
ENHANCED MAINTENANCE The truck-mounted jetting units enhance the capability to efficiently clear stormwater drains and sewerage systems
Severe flooding events along South Africa’s coastal regions have underscored the crucial role of resilient infrastructure in managing excessive rainfall, says pumps supplier Werner Pumps, which has committed to delivering 50 custom-built vehicles, at five vehicles a month, to a municipality in KwaZulu-Natal, as a proactive measure.
The municipality commissioned the truck-mounted jetting units to enhance the capability to efficiently clear stormwater drains and sewerage systems within its jurisdiction.
Neglected stormwater drains can lead to debris accumulation, causing water to seep underground and, potentially, lead to significant structural issues, such as sinkholes, says Werner Pumps MD Sebastian Werner.
Similarly, blocked sewers also pose a threat to public health by increasing the risk of sewage overflow onto streets and other public areas.
Therefore, he emphasises the importance of these units in the aftermath of flooding and for routine maintenance activities.
A distinctive feature of the units produced for the KwaZulu-Natal municipality is the inclusion of crew cabs, consequently allowing for maintenance teams to be transported along maintenance routes efficiently. This innovation underscores the company’s commitment to delivering cost-effective, labour-saving solutions.
The decision to expand the order for these units followed the municipality’s positive experience with an initial batch, which “demonstrated the quality and effectiveness of [Werner Pumps’] equipment”, adds Werner.
Customisation options for the truck-mounted jetting units include power take-off or donkey-engine-driven systems, various tank materials and sizes, as well as a range of side-mounted accessories and hose reel configurations. The units are available in 6 000-ℓ, 10 000-ℓ and 15 000-ℓ sizes.
Werner Pumps supplies a range of accessories for all its units, including low-water inlet switches, high-pressure jetting hoses (20 m, 30 m, 50 m, 120 m or 180 m), high-pressure guns with lances, nozzle holders and fan nozzles.
“This level of customisation ensures that every unit can be tailored to meet the specific requirements of different operational contexts,” Werner notes, adding that the company “does its best” to meet all customers’ high-pressure jetting and vacuuming requirements.
The company can also advise customers on how best to service a particular application.
Meanwhile using high-quality components, such as HP pumps and 304 stainless steel in the manufacturing process, means that there will be little maintenance requirements, says Werner Pumps sales manager George Jolly.
These materials are chosen for their durability and resistance to corrosion, particularly in coastal environments, while the innovative feature of including solar-powered battery chargers for every truck ensures continuous battery charging, even when the vehicles are not in use, he explains.
“The HP pumps, and our trucks overall, have very little maintenance requirements, which allows for streamlined and cost-effective operations.”
Comprehensive Customisation
Werner Pumps offers comprehensive operator training and certification, ensuring that local governments and other stakeholders receive equipment that exceeds specifications.
The company's design and manufacturing capabilities enable it to manufacture equipment tailored to client specifications, including environment-friendly options that eliminate the use of harsh chemicals when clearing blockages.
Despite the challenge of manufacturing over 50 units within a stringent timeline, Werner Pumps adapted its operations to meet the client’s needs, despite it placing the company’s factory under “tremendous pressure”.
Operator negligence and abuse of equipment is also a challenge, which the company is trying to mitigate by supplying a training video on the various units to the municipality, for further operator refresher training.
Further, the company is considering further development of its Amanzi Recycling Combi Vac/Jet trucks, which feature water-recycling capabilities, potentially saving up to 165 000 ℓ of fresh water for every eight-hour shift.
This approach not only conserves water but also reduces fuel consumption and maintenance costs, Jolly highlights, noting that this further demonstrates Werner Pumps’ commitment to sustainable, efficient infrastructure maintenance solutions.
Werner Pumps fabricates all jetting and vacuum equipment in South Africa, consequently supporting the local economy and ensuring that the products are
well suited to the unique environmental conditions of the country.